Subproject T5: Support of stakeholders in the interdisciplinary life-cycle-accompanying innovation process of Product-Service-Systems (PSS) using the example of large-scale plants in the steel and non-ferrous metals industry “Knowledge Transfer Project”
The aim of Subproject T5 is development, implementation, and evaluation of scalable Engineering and Operation Support Systems (EOS²) to support interdisciplinary innovation cycles of large industrial plants in the steel and non-ferrous metals industry. An evolving digital twin aggregates, from the manufacturer’s point of view, the models of a plant with operating data and design changes during operation. It enables existing engineering solutions (Hidden Innovations) to be found while creating the platform for services of the plant as Product-Service-System (PSS), so that customers can, for example, use simulation models to ensure structural or procedural changes.
Motivation
- The increasing demands of customers result in a great increase of complexity in the development process and in life-cycle management.
- Strong dependencies and interactions between formerly seperated development areas
- An increased need for coordination between the disciplines
- During the development process, customer-specific adaptations of the machines and systems lead to innovation in the form of special solutions. Constructive measures cannot yet be systematically recorded and therefore cannot be carried out systematically after the construction has been completed.
- Reduce the development costs of the digital twins through the consistent use of simulation environments and equipment models.
- Enable multi-phase information and knowledge management through an evolving digital twin.
Prospective Results of the Transfer Project
- Reduction of own expenditures for supplies of new plants and modernization by at least 20% through systematic, interdisciplinary engineering. Increasing the quality of supplies while simultaneously reducing throughput times by 20%.
- Reduction and acceleration of own engineering expenditures for new plants and modernization by at least 10% through interdisciplinary mechatronic engineering.
- Prototype development and validation (by/with an operator) of at least one of the digital business models such as Service Digital Twin, Plant Asset Management, Simulation and Digital Training over the course of the production system’s useful life.
Selected publications
- S. Feldmann, S. Herzig, K. Kernschmidt, T. Wolfenstetter, D. Kammerl, A. Qamar, U. Lindemann, H. Krcmar, C. Paredis, B. Vogel-Heuser: Towards Effective Management of Inconsistencies in Model-Based Engineering of Automated Production Systems, In: 15th IFAC Symposium on Information Control in Manufacturing (INCOM), Ottawa, Kanada, pp. 916–923, 2015
- K. Kernschmidt, T. Wolfenstetter, C. Münzberg, D. Kammerl, S. Goswami, U. Lindemann, H. Krcmar, B. Vogel-Heuser: Concept for an Integration-framework to Enable the Crossdisciplinary Development of Product-Service Systems, In: IEEE International Conference on Industrial Engineering and Engineering Management, Bangkok, Thailand, 2013
- J. Reif, G. Koltun, T. Drewlani, M. Zaggl, N. Kattner, C. Dengler, M. Basirati, H. Bauer, H. Krcmar, K. Kugler, B. Lohmann, U. Meyer, G. Reinhart, B. Vogel-Heuser: Modeling as the Basis for Innovation Cycle Management of PSS: Making Use of Interdisciplinary Models, angenommenes paper in IEEE International Symposium on Systems Engineering (ISSE) 2017, IEEE, Oct. 2017
- S. Feldmann, M. Wimmer, K. Kernschmidt, B. Vogel-Heuser: A Comprehensive Approach for Managing Inter-Model Inconsistencies in Automated Production Systems Engineering, In: 12th IEEE International Conference on Automation Science and Engineering (CASE), Fort Worth, USA, pp. 1120–1127, 2016
- G. Koltun, S. Feldmann, D. Schütz, B. Vogel-Heuser: Model-Document Coupling in aPS Engineering: Challenges and Requirements Engineering Use Case, In: IEEE International Conference on Industrial Technology (ICIT) - 2017, Toronto, Canada, pp. 1177–1182, 2017
- M. Böhm, J. Weking, F. Fortunat, S. Müller, I. Welpe, H. Krcmar: The Business Model DNA: Towards an Approach for Predicting Business Model Success, Internationale Tagung Wirtschaftsinformatik (WI), St. Gallen, Schweiz, 2017
- F. Elezi, A. Sharafi, A. Mirson, P. Wolf, H. Krcmar, U. Lindemann: A Knowledge Discovery in Databases (KDD) Approach for Extracting Causes of Iterations in Engineering Change Orders, In: ASME 2011 International Design Engineering Technical Conferences & Computers and Information in Engineering Conference IDETC/CIE, Washington DC, USA, 2011
- T. Wolfenstetter, S. Bründl, K. J. Füller, M. Böhm, H. Krcmar: Towards a Requirements Traceability Reference Model for Product Service Systems, 6th International Conference on Industrial Engineering and Systems Management (IEEE-IESM), Sevilla, Spanien, 2015
- O. Hofmann: Entwicklung und Realisierung einer Virtuellen Compact Strip Production Gießwalz-anlage, Shaker Verlag, Aachen, Zugl. Dissertationsschrift RWTH Aachen, 2012
- C. Plociennik: Konzeptionelle Ansätze zur ganzheitlichen Betrachtung von Produktionsanlagen am Beispiel der Walzwerksindustrie, Shaker Verlag, Aachen, Zugl. Dissertationsschrift RWTH Aachen, 2014

Prof. Dr.-Ing. Birgit Vogel-Heuser
Coordinator of the CRC 768
Subprojects A6, D1, D2, T3, T5 and Z
Institute of Automation and Information Systems
vogel-heuser@tum.de
Tel.: +49 (0) 89 289 16400
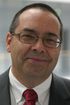
Prof. Dr. Helmut Krcmar
Subprojects A4, C1, D1 and T5
Chair for Information Systems
krcmar@in.tum.tum.de
Tel.: +49 (0) 89 289 19530

Felix Ocker M. Sc.
Subprojekt T5
Institute of Automation and Information Systems
felix.ocker@tum.de
Tel.: +49 (0) 89 289 16446
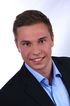
Matthias Seitz, M.Sc.
Subproject T5
Institute of Automation and Information Systems
matthias.seitz@tum.de
Tel.: +49 (0) 89 289 16429